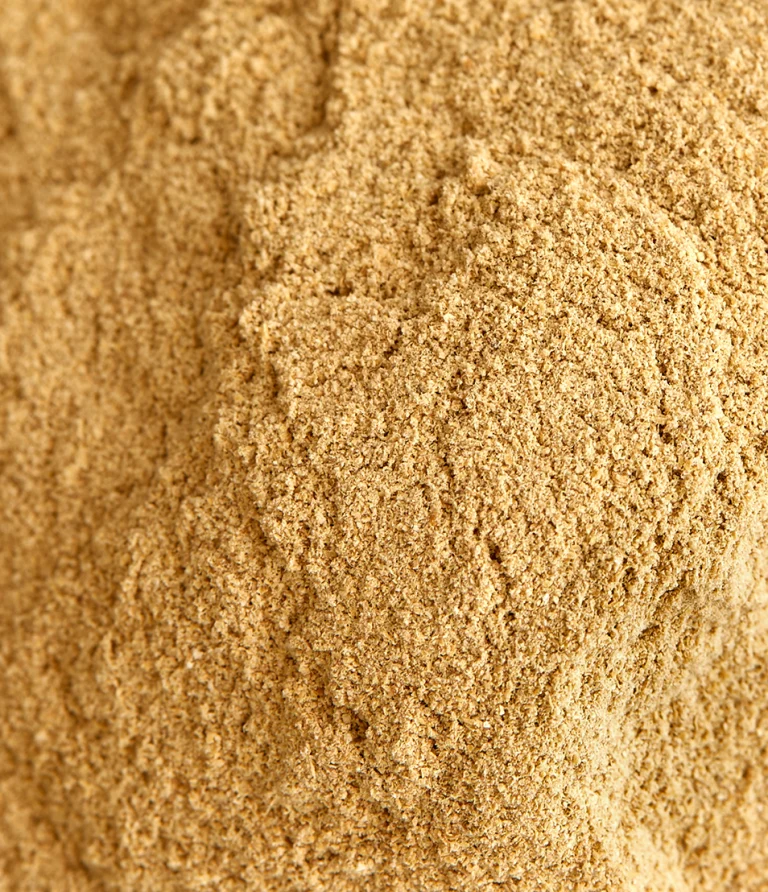
ENVIRONMENTALLY
FRIENDLY MATERIALS FOR
A NEW ERA OF
COSMETICS PACKAGING
ENVIRONMENTALLY-FRIENDLY
MATERIALS FOR A NEW ERA
OF COSMETIC PACKAGING
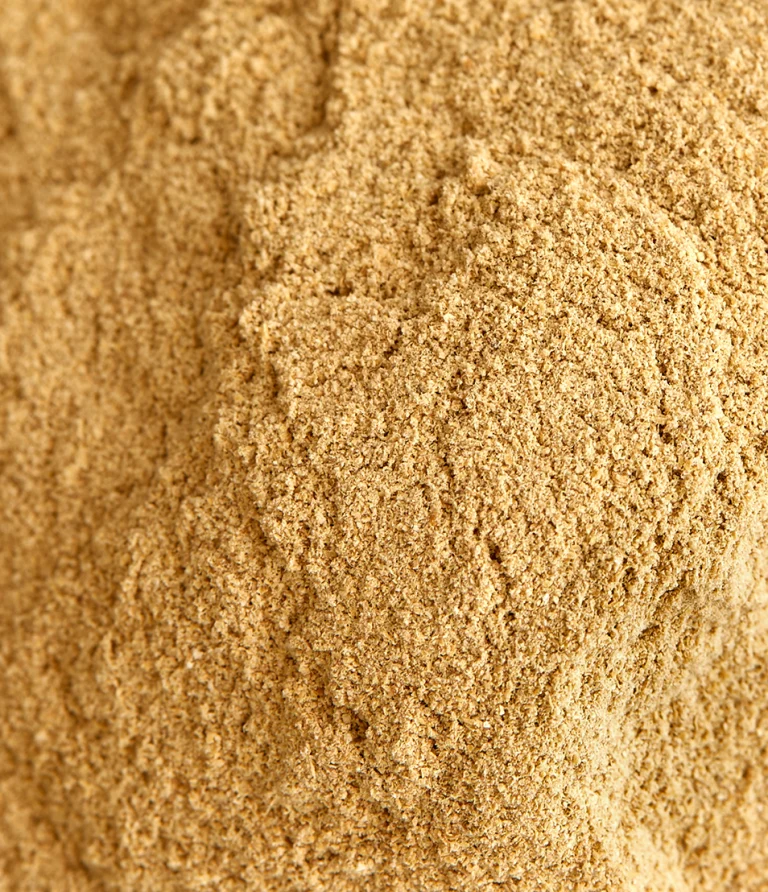
Oryzite adapted to the cosmetics industry
All our eco-friendly materials are based on Oryzite and apply our knowledge and years of experience in cosmetics. These factors allow us to research, experiment and innovate towards a common goal: developing the most environmentally friendly materials for any cosmetic packaging solution, bearing in mind the specific requirements of the sector.
Thanks to our innovative process to create our sustainable cosmetic packaging materials, we can modulate the percentage of Oryzite according to the client’s needs, but always aiming to respond to their objectives and ideas in the most sustainable way possible.
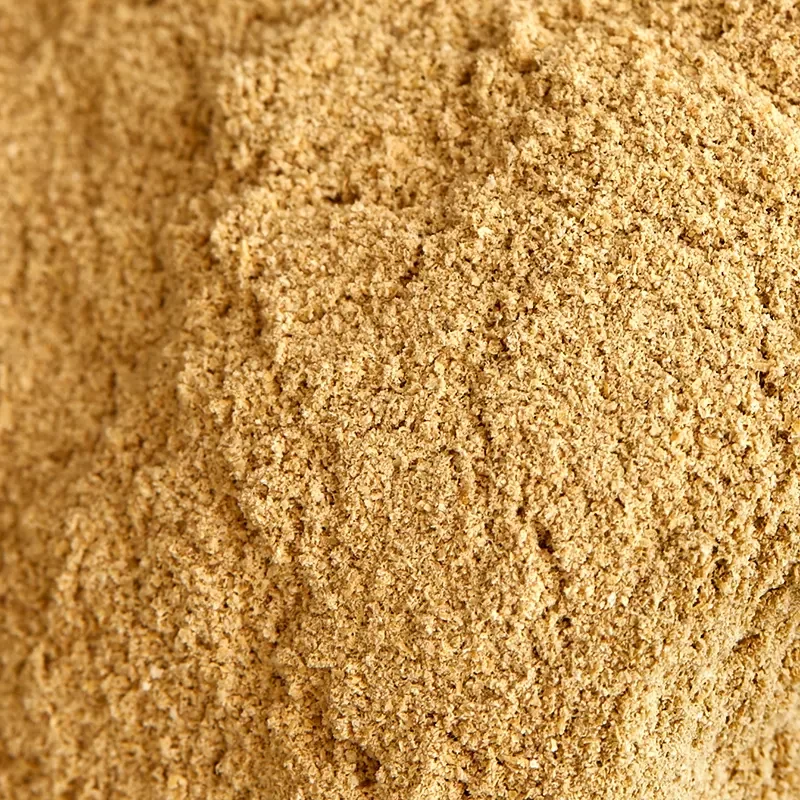
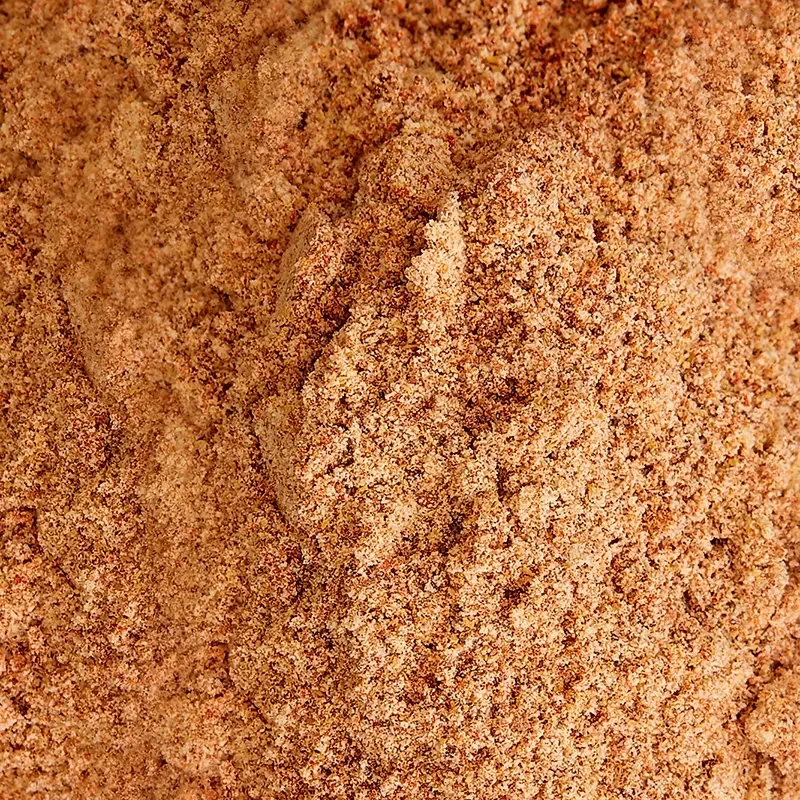
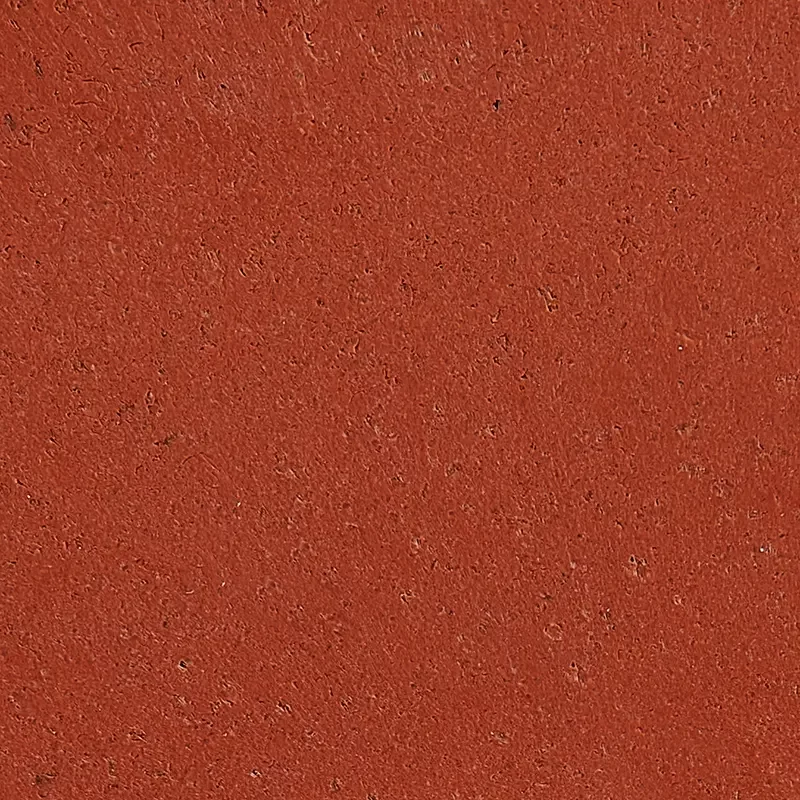
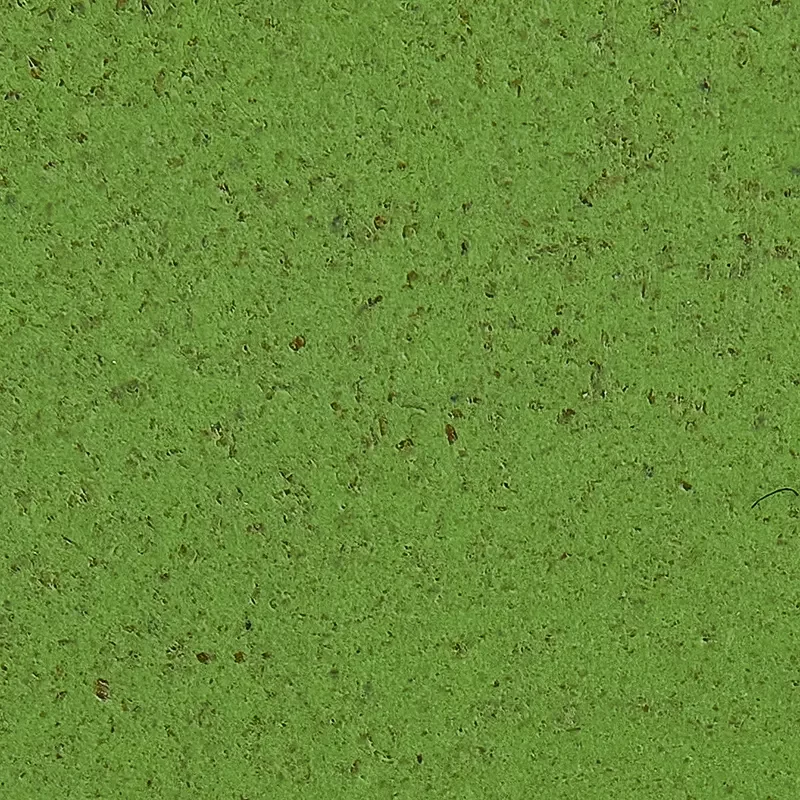
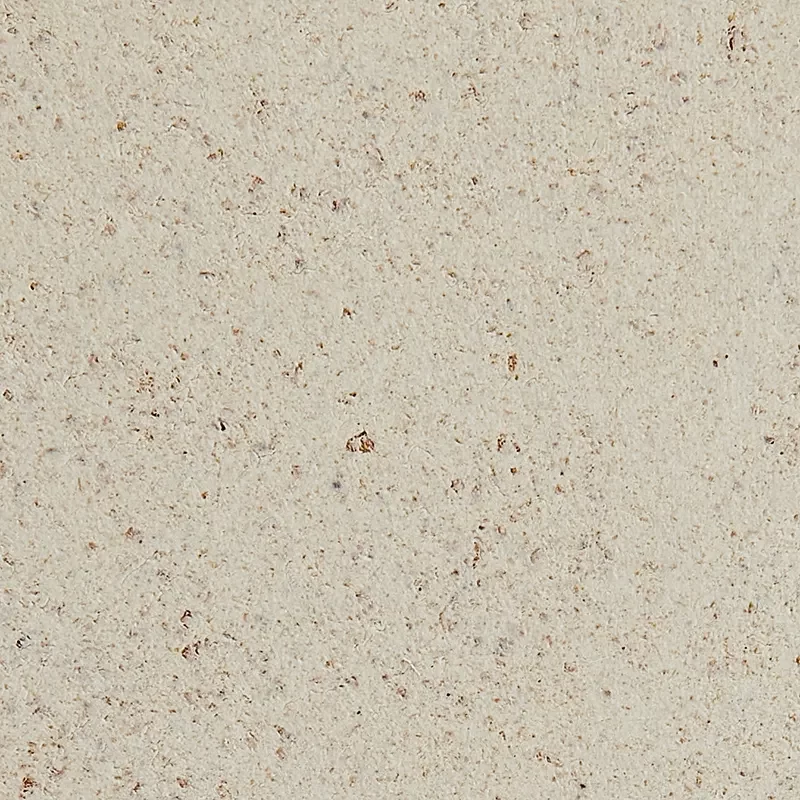
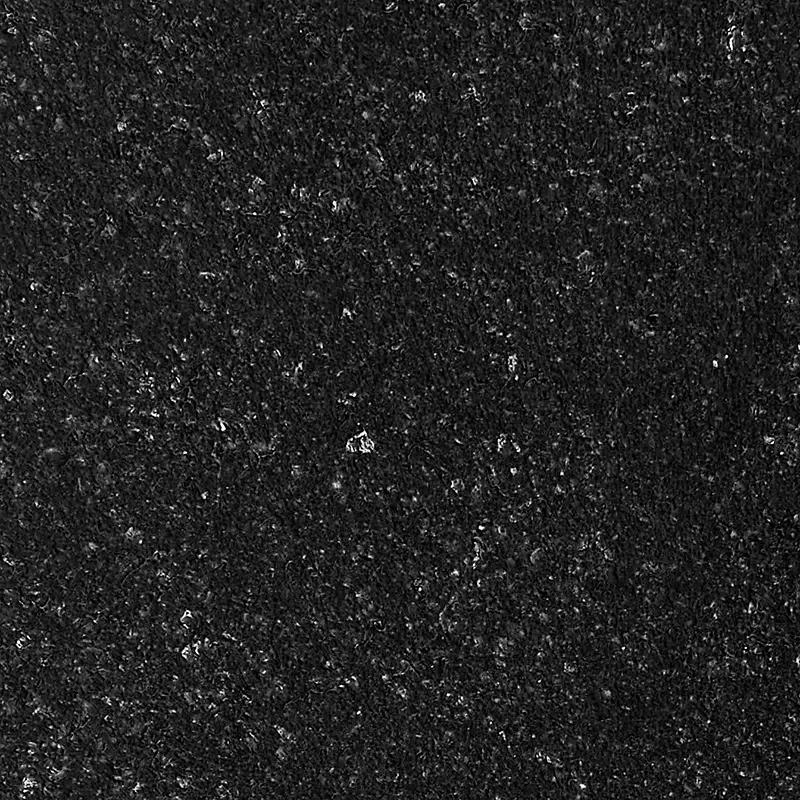
Akoa
Oryzite (rice husk) + any type of polymer

POSITIVE IMPACT ON THE ENVIRONMENT
Replaces up to 92% of plastic with Oryzite (rice husk).
Reduction in CO2.
Recyclable and reusable.
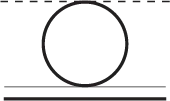
TECHNICAL PROPERTIES
Oryzite improves the characteristics of any polymer: plasticity, strength, low thermal conductivity, lightness, product protection, etc.

USES IN COSMETICS
With our eco-friendly material Akoa, we produce standard containers (Barcelona Collection) or tailor-made cosmetic packaging adapted to our clients’ needs, such as personalised jars, lids, caps, bottle collars, boxes, and cases for make-up, eye liners and lipsticks.
Norava
Oryzite (rice husk) + biodegradable polymer

POSITIVE IMPACT ON THE ENVIRONMENT
Replaces up to 92% of plastic with Oryzite (rice husk).
Biodegradable and compostable.
Reduction in CO2.
Recyclable and reusable.
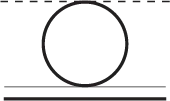
TECHNICAL PROPERTIES
Oryzite improves the characteristics of any polymer: plasticity, strength, low thermal conductivity, lightness, product protection, etc.

USES IN COSMETICS
With our eco-friendly material Norava, we produce sustainable standard containers (Barcelona Collection) or tailor-made cosmetic packaging adapted to our clients’ needs, such as personalised jars, lids, caps, bottle collars, boxes, and cases for make-up, eye liners and lipsticks.
A unique technological process
Oryzite production
The manufacture of our eco-friendly materials begins with the production of Oryzite, a sustainable alternative to plastic, using an enzymatic process that catalyses the rice husk through temperature and pressure. The result is Oryzite, a sustainable product with thermoplastic properties.
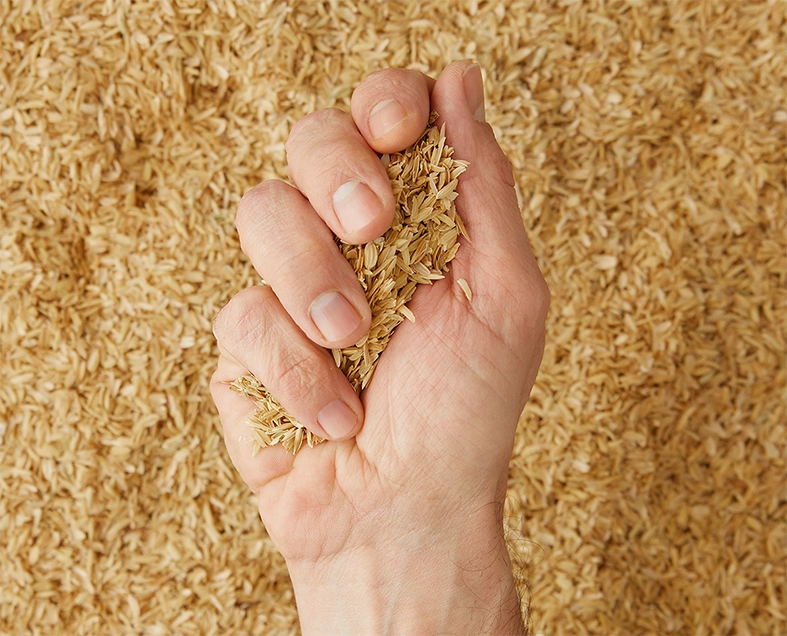
Manufacturing our materials
Once the Oryzite is produced, our eco-friendly cosmetic packaging materials are developed using the innovative Akilorit technology process.
Currently, the manufacturing process for most fossil and non-fossil plastic parts usually starts with a compounding process that consists of mixing polymers and additives. This is done by special companies, separate from the final processing plants. However, we use an autonomous, efficient and sustainable process to create our eco-friendly materials for cosmetic packaging.
Akilorit is Oryzite’s patented technology designed to incorporate biofillers into polymer resins in an energy-efficient process that drastically reduces CO2 emissions:
1. Manufacturing steps are eliminated and improved (reducing energy consumption by up to 92%).
2. The logistics chain is simplified, as the compounding activity is carried out in our own manufacturing centre for sustainable cosmetic packaging.
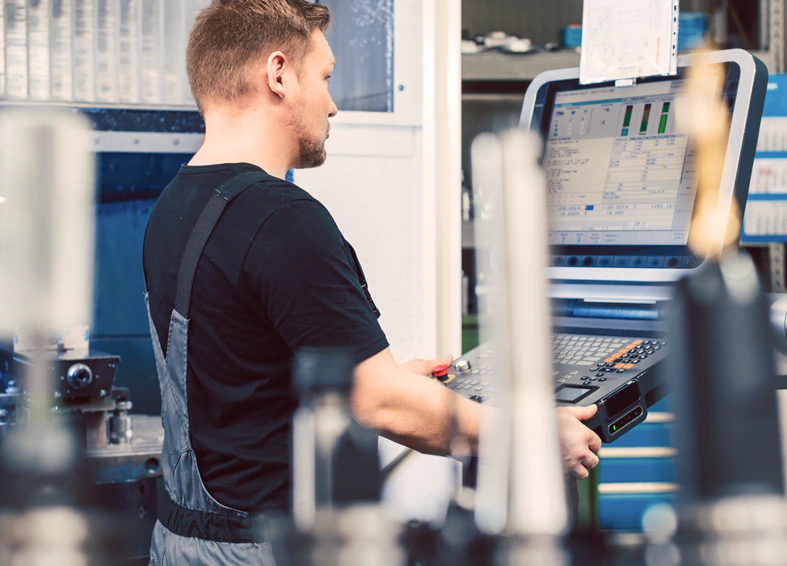
Akilorit technology step-by-step
STEP 1. Preparing the formulation
The desired formulation for the material is prepared based on the quantities of Oryzite and polymer required. Without the prior need for drying, the raw material is added to a customised premixer to create a homogeneous composition.
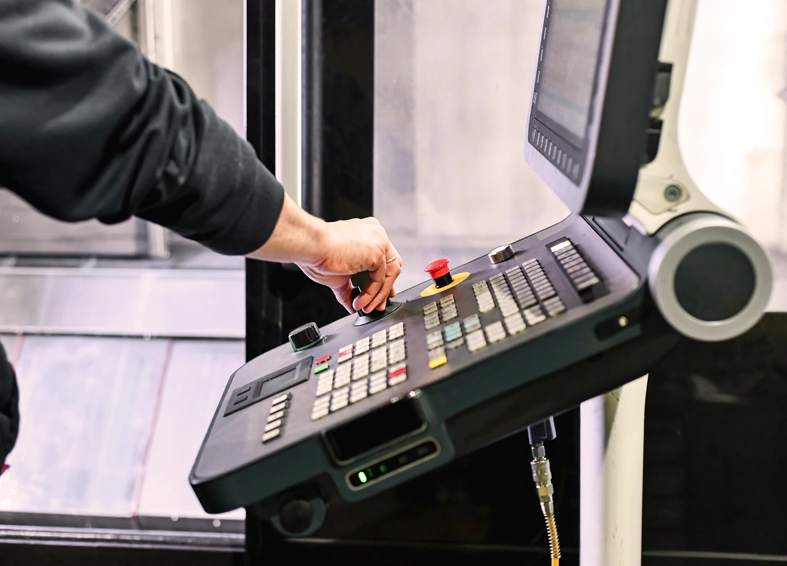
Akilorit technology step-by-step
STEP 2. Homogeneous mixture
Heat is applied to the premixed material to grind or crush the polymer into microscopic pieces, to ensure a totally homogeneous and efficient mixture of the components. Much less energy is consumed than in conventional processes.
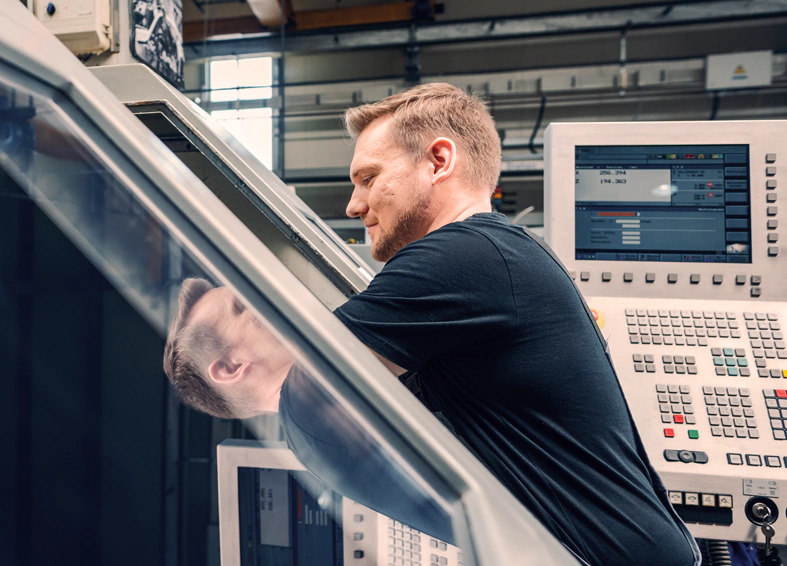
Akilorit technology step-by-step
STEP 3. Final processing
Hot granules are sent directly to a thermal treatment oven to extract moisture at the required level, under 100 pm of H20, in the least amount of time possible (only 10 minutes), so we save energy and reduce CO2 emissions.
Finally, in the same facilities as the material is produced, different products for the cosmetics industry, jars, caps, sheets, etc. are manufactured. The goal here is to simplify the logistics chain, thereby reducing our CO2 footprint.
How do our materials allow us to provide customised sustainable cosmetic packaging solutions?